Product recalls are a veritable nightmare!
There is no other way to express the dread and that sinking feeling when the customer complaints start rolling in, and you begin considering whether or not to announce a recall.
A recall will spell significant damage to your brand image, and thousands, if not millions of loss in revenue.
Yes, you may argue that retailers are insured against recalls, but building trust with your customers is a difficult task at the best of times.
The digital age has also made it more difficult to hide the smallest of quality problems from your customers, and rebuilding trust from slip-ups that could have been prevented just adds fuel to a fire that won’t stop burning.
But it’s not all doom and gloom…
Product recalls can be prevented through best practice QC procedures, through due diligence, through strategic planning and implementation, through proper inspection reports and appropriate product testing to ensure that your compliance issues are a thing of the past.
In this blog post, we take a look at four product recalls from household goods and electronic giants in recent history, that could have been prevented through a bit of due diligence, through proper testing procedures and reliable quality management service providers.
1. Keurig Coffee Makers To Pay $5.8 Million In Civil Penalties
Keurig is a well-known coffee machine brand in the United States, with many corporate offices around the country being dotted with these machines, where it fast became an office staple.
But, imagine this.
Waking up to make that quick cup of coffee before work, or even offering an important investor a cup of coffee before heading into a meeting, and your machine begins to steam and spit out boiling water, causing a potential burn injury.
Not an ideal situation…
This left Keurig in some seriously ‘hot water’!

On 23rd December 2014, the Consumer Product Safety Commission (CPSC) announced the recall of over 7 million coffee machines.Between 2010-2014, there were over 200 complaints of boiling water spraying out of the machine and approximately 90 burn injuries reported.It has been recently announced that Keurig has
agreed to pay over $5.8 million in civil penalties to the government.
This penalty is to settle the charges against Keurig as they knew about the product’s defect, but failed to report it and continued to export the product despite the fact that it can and did cause major injuries.
What should have been done differently?
Keurig appealed to consumers to request a repair kit that was able to fit onto the product free of charge.
In reviewing the repair kit installation guidelines, it consisted of a new basket with a rubber seal to ensure that no hot water or steam would escape during use causing potential for burn injuries.
There was also an extra handle that slides over the original one to avoid direct contact with the hot water or steam that may be released when the handle is in position, or if hot water or steam is released during use, it would be pushed in the downward or upward position.
This kind of repair kit tells us that problem was related to product design more than any manufacturing or quality control issues.
This story also tells us how that at times it may not be enough to be in compliance with just the testing regulation.
There may be times when specific tests need to be developed to beyond the standard testing criteria, simulation tests are often a good example here; where a quality control team can simulate the kind of tough operating environment that a specific product may need.
This can often be done through a thorough risk assessment that should be completed during the product design stage.
The CPSC has not been able to disclose any more information as to what caused the defects, but that Keurig has agreed to
build and implement a compliance program to ensure that they comply with the Consumer Product Safety Act.
Adopting a compliance program stands as the rules, standards, regulations and requirements your organization sets for its suppliers, as this will grant you full transparency into supply chain operations.
A compliance program should not just be another program that importers tick off on an annual basis. It should become a key outcome and a reflection of an effective and efficient organization.
The key to a successful compliance program will be how well you can integrate compliance procedures into every facet of your brand.
2. Hasbro Recalls 1 Million Easy Bake Ovens
You have found that perfect Christmas gift for your little ones.
One that will create all those cute little memories that you will hold onto for a lifetime.
Then, a cry for help as their hand is stuck inside the toy under the element, causing some serious injury.
Quite far from a ‘Merry’ Christmas…
Hasbro was in deep with
over 1 million easy bake ovens that were recalled and over 77 reports of injury, and a report of one five year old being burnt so terribly that a partial finger amputation was needed.
What should have been done differently?
There was a finger entrapment test that was developed under the ASTM F963 as an industrial standard, but which only came into regulation in 2013 under the
Consumer Product Safety Improvement Act (CPSIA).
Currently, all
toys and children’s products need to be designed to comply with this ASTM F963 standard.
Retailers should be requesting that their manufacturers and suppliers need to be testing in compliance with this regulation, and have to be passed through an accredited third party lab before mass production can begin.
In meeting this criteria, there will also have to be a double check; either during inspection or through the lab with a random sample that is picked during the inspection process.
Procedures like this help to minimize potential risk and recall of a noncompliant product.
3. Sony To Pay $19 Million Dollars in Battery Recall
Exploding Dell notebooks with non-compliant Sony batteries.
A match made in retail hell.
4.1 million batteries in Dell notebooks needed to be recalled for overheating and potentially catching fire.
Research says that this was due to metallic particles being present in the critical parts of the batteries, at certain times causing instability in the battery.
These batteries were not only used in Dell computers, but other brands like Apple as well, so they recalled over 10 million batteries in total.
Sony has recently
agreed to pay $19 million dollars as settlements to this ongoing lawsuit.
What could have been done differently?
It has been said that the reason for this potential hazard was due to the presence of metallic particles, in the battery, in particular; nickel was found in these batteries. It unexpectedly got into the battery during the manufacturing process during two stages of the production process.
Here we can assess that the factory’s quality systems should have been reviewed and as to whether or not their QC team followed best practice in identifying potential defects.
There may have been bad storage practices causing a mix up between defective products and good one’s.

A root-cause analysis would have been needed to adjust the production line to fix the problem. Once this analysis is completed and amendments made by the retailer, a third party representative would need to validate the preventative and corrective action for the defect.
Factory audits can be an essential to safeguarding against product defects and recalls.
Practice due diligence here, ensure your quality control team is on top form and up to date with the latest in testing and regulation.
4. Fidget Spinners – Over 200 000 Have Been Recalled!
The latest craze amongst children all over the world.
The invention was originally intended to improve fine motor skills in children with learning disabilities, but grew in its popularity faster than what one could even blink.
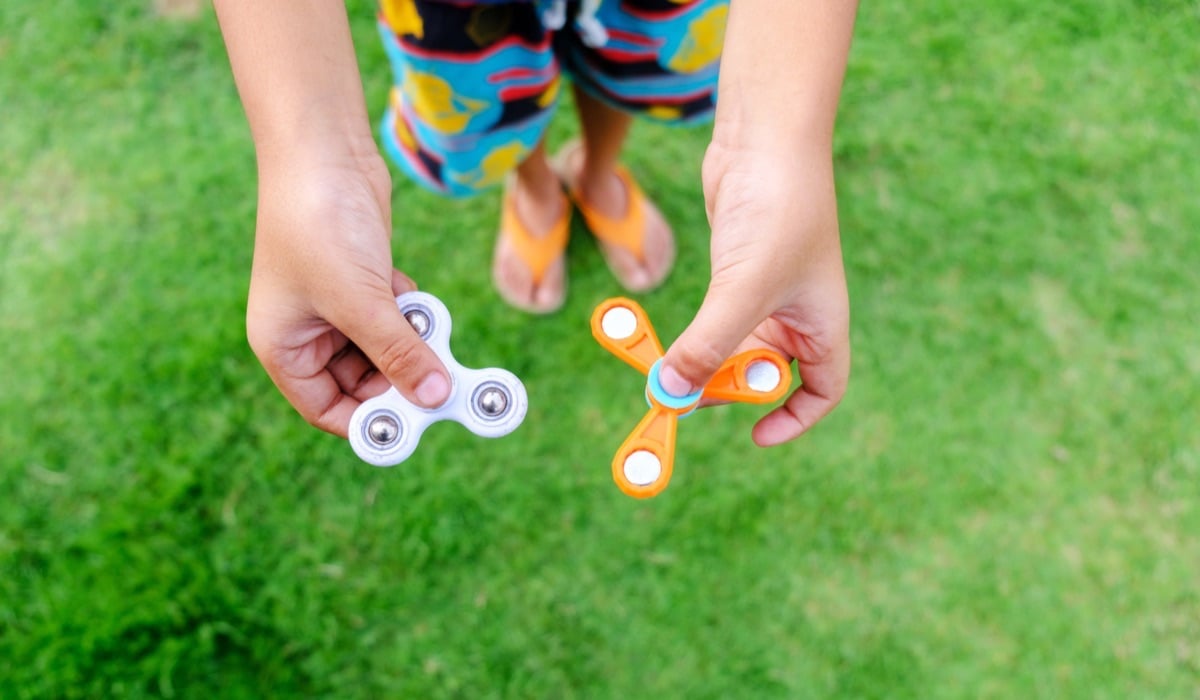
In fact, the inventor today does not get a dime out of the sales of this popular children’s toy, as she was told her idea was not good enough and wouldn’t sell. Needless to say, millions of these toys are sold the world over.
But, she could count that as somewhat of a blessing…
Recently, over
200, 000 of them had to be recalled as they caused major harm to many children, with fingers getting stuck in the outer bearings to smaller parts being swallowed, where surgery was needed.
What could have been done differently?
This toy is specific in the types of international regulation and compliance that it needs to meet, but not many retailers can provide the necessary compliance documentation for this product.
It has been urged to rather seek out the compliant toys with all the necessary risk and warning labels on them.
As per international standard for general toys, it is required to drop this toy a few times only. This dropping of the toy often does not take into consideration just how often children drop these spinners. These spinners are dropped multiple times a day by end users, so this test in fact may not represent an adequate simulation.
A factory should be creating tough testing procedures to simulate the type of environment this toy will likely be exposed to.
These tests need to go beyond the standard testing criteria to ensure a durable, safe spinner is found in your children’s hands.
Apart from the strict QC procedures that should have been conducted, the correct lab tests should have been followed, as some spinners (the ones with batteries) were found to have high levels of lead present, posing a threat to its end consumers.
The appropriate chemical tests should have been performed to identify these chemical risks early on, giving your supplier time to rework the product to meet its compliance standards.
Conclusion
Strict quality control procedures need to be followed.
By ensuring you follow QC best practices for your product you begin to safeguard your brand, your product and even your end-consumer from a potentially bad quality product that can injure them, and cost you millions in revenue.
If you are not using a third party quality provider for all your testing and compliance procedures conducting things like; pre-purchase testing and inline inspections can be key to identifying these defects early on.
A bit of due diligence and strict QC procedures can go a long way in saving you the terrifying reality of product recalls and persistant compliance issues.
There are More Lessons To Be Learnt In This Case Study!
Are you ready to begin optimizing your processes?