Finding a surefire way to prevent product defects and reduce them to zero is what good dreams are made of, but, sadly, the reality is usually closer to somewhat of a living nightmare for most importers.
The hard truth is that without taking a systematic approach to tackling the production aspect of your supply chain from the very outset it will put your entire operation at risk.
In this post we seek to help outline 7 specific steps that you can take to minimise the amount of product defects that you experience during your entire production process, all in the hope of preventing product defects, but also helping you take a more collaborative approach to dealing with your suppliers.
When things start to go wrong
It may happen that you’ll receive a batch of products with the incorrect dimensions, the wrong color stitching on a couch or become aware that the incorrect tests were done, resulting in non-compliance and regulations not being met.
Meanwhile…
Your shipment is now delayed (or worse), possibly
stuck in customs and the mountain of problems and paperwork just keeps stacking up, a domino effect of production issues with no light at the end of the tunnel.
So, what can you do to prevent product defects all together?
It all starts with these 7 steps:
- Communicating product requirements with your QC staff and suppliers
- Communicating your specific requirements for packaging
- Defining onsite tests and inline tests with your supplier and factory
- Defining your classification terminology with your supplier
- Establishing a perfect sample
- Conducting DUPRO quality control
- Conducting after production quality control
Communicating your product requirements with your QC staff and suppliers can help prevent quality defects
Communicating your product specification with your supplier is essential to safe guarding against product defects.
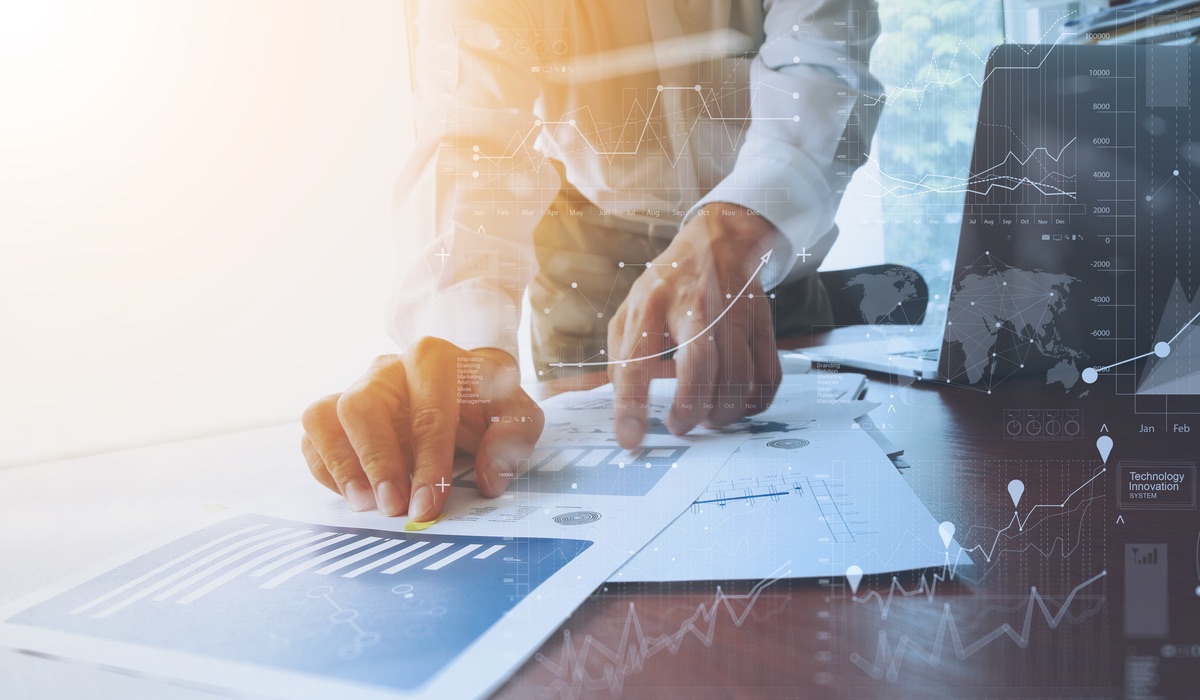
Product specification can look anything like your products dimensions, the volume, it’s weight, the color and any specific labeling that it may need to meet regulation.
In your specifications you need to ensure that you are as specific as you can possibly be, from specific color palettes to the maximum weight of an electric blender. The more specific you are, the easier it will be for your supplier to meet your specifications.
These specifications will also provide your supplier’s quality control team with a standard/guide to monitor the production of the item appropriately.
This is where the
in-house vs outsourced inspection arguments come in.
You need to establish whether an in-house team is fully capable of conducting all of the appropriate tests and reporting that is needed for your product, or whether it will be of greater benefit to outsource the professional expertise to a third party quality provider.
As an importer, you need to ensure that you are up to date with all the latest regulation that is specific to your product.
Are you?
{{cta(‘37580c78-0398-44e8-8f88-7682a9c94777′,’justifycenter’)}}
Communicate your packaging requirements to Prevent product defects
Your product needs to meet packaging requirements when shipped.
This will often mean that all the necessary documentation will be present and/or visible on the package during the import and export customs process.
You need to specify the packaging requirements and what exactly needs to be present on the outside of the box. This will safeguard against possible damage during shipment, ensuring their safe arrival.
What onsite tests and checks will you be doing?
Your quality control team, whether an in-house or outsourced team, have to be informed about the types of quality tests that need to be conducted on site.
Once you confirm what tests are needed, your inspection team will need to know what testing equipment is needed per product.
An electrical juicer for example will be tested differently to what tests will be needed for other product categories.
If you choose to use an
experienced third party quality provider you will be able to leverage their technical expertise, for example, the exact type of load testing that may be needed for a couch that is destined for the European market.
An experienced third party provider will also have labs with controlled environments and all the right equipment to test your product, along with the constant monitoring of any updates in regulation that you may need to be aware of.
Have you agreed upon the defect classification terminology?
Many importers choose to use the following classification terminology when dealing with their suppliers:
A critical defect – This is defined when the product may cause possible injury or harm to the end user. This product’s safety is compromised.
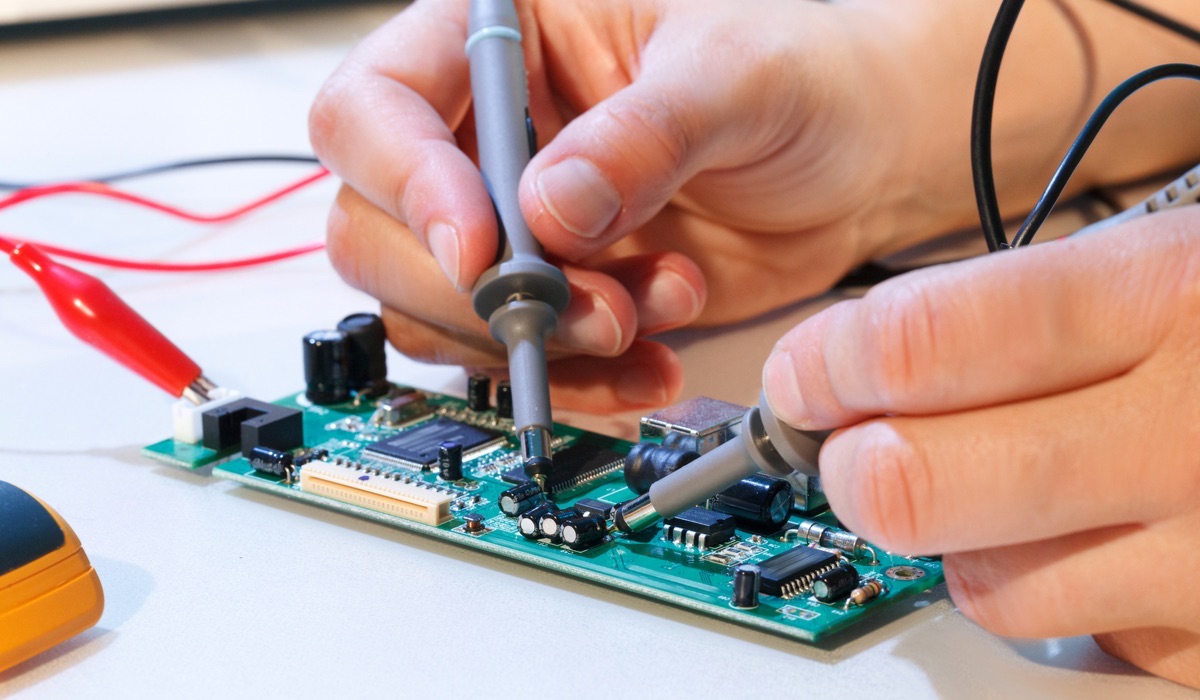
A laptop’s battery overheating that when unattended whilst charging can cause fires would be classified as a critical defect.
Where the product in question can cause injury to the end user, this results in product recalls and is hugely damaging to your brand.
A major defect – This is defined when its condition will affect the sale of the product in the marketplace, likely resulting in the end user returning it with dissatisfaction.
A coffee maker that does not heat the water adequately to make a decent, drinkable cup of coffee is classified as a major defect.
This product has caused dissatisfaction amongst its end users and they then return it to the store, likely reviewing the product online, which will have an impact on the future sales of that item.
A minor defect – This is defined when its defect is small, and will not affect its saleability in the marketplace and does not pose any harm or injury on the end user.
Take a wooden coffee table for example. Your quality control teams takes the product through its tests and they come across a scratch underneath the table.
This is a scratch that your end user will not see in normal use of the product or may never even see it for that matter. This is what we would classify as a minor defect where this product will still go to market as it will not cause any damage or harm to the end user.
But that’s not all…
What about a sample?
I have left obtaining a sample for the end…as some importers don’t require a sample before production.
While this is not a necessity, by adding this into your production procedure
it can help you significantly reduce product defects that come from your selected supplier and factory.
Once you have established the appropriate product requirements, you can then request a sample from your supplier.
Once you receive your sample you need to analyze it and ensure that it meets all of your requirements, and then send it back to your supplier with either a confirmation to go ahead with your production, or with a list of further specifications that they need to meet.
Well, what happens if it doesn’t meet your requirements?
Samples will not always meet your specified product requirements.
Often times you can catch this just by holding or looking at the product. But, more often than not a substandard product of will reach the end consumer opening your brand up to severe damage and risk.
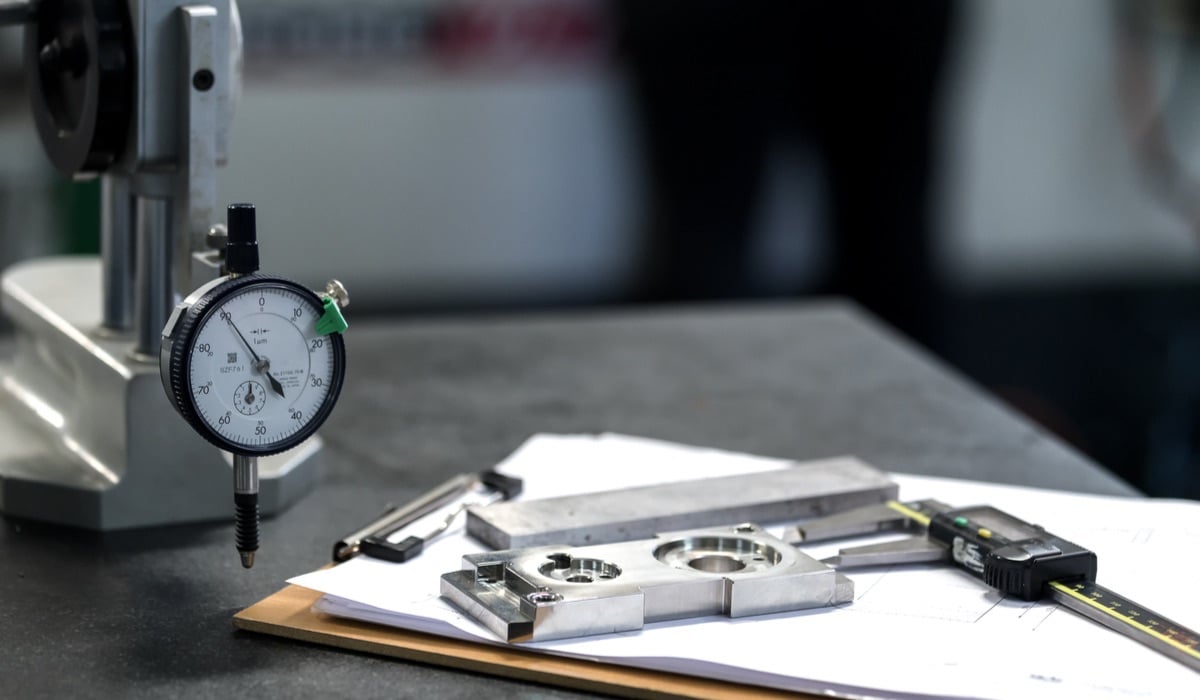
Therefore an important question you should be asking your supplier before all this is, how they will go about preventing any quality issues that may arise during your operation?
Understanding how your supplier handles quality pressures and compliance procedures will help define what kind of relationship you have with them.
Before mass production, your supplier needs to provide you with a
technical compliance folder (TCF) which must contain full compliance reports from physical safety reports, to chemical safety to electrical safety.
For any missing reports, your sample product will need to go through all of the testing procedures that is required to meet specific levels of compliance for your destination country.
If after being tested and analyzed it does not pass the minimum requirements needed for the product, your factory should be able to provide you with
a root cause analysis to address what went wrong and then advise on any corrective or preventive action plan.
From here they will be able to make the adjustments as needed and you may also want them to send you another sample after they have made the adjustments that you specified.
How to manage quality during your mass production process?
During the production process, there is often a variation in the quality of the products.
This is why you should be employing a factory quality control team to minimize this scope of variation.
This team does this through inline production checks that will identify any defects that can be amended on the production line.
During your supplier selection phase you would have done an analysis on the success rate of your factory. This will help you determine whether or not you should outsource your inline inspections to a qualified third party quality provider.
Their production line expertise will help raise the level of the overall quality system of the factory, therefore minimizing the number of product defects coming out of the factory.
You can also secure the quality of your production through final inspection controls
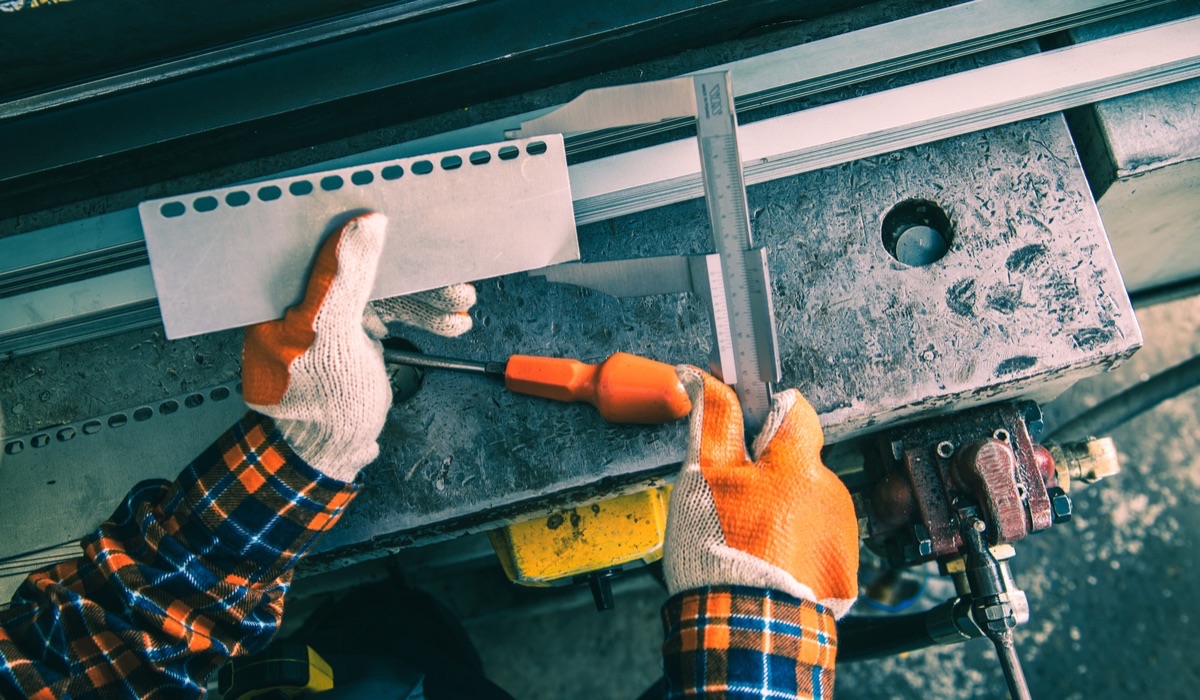
Managing product defects can also be addressed after mass production through a
Final Random Inspection to check to filter out any last defects within your products.
Often times samples are drawn after mass production for chemical testing and again during your first shipment and also in the case of a re-order shipment.
Doing chemical tests on samples during these three stages is a way of ensuring that your products are still in compliance as contamination may have occurred on the production line or during your shipment process.
Key Takeaways
Product defects are not ideal, suppliers hate them as much, if not more than you do.
By following the guide laid out above, you will be setting a solid foundation on which to begin minimizing the amount of product defects that you experience.
So let’s round this all up:
- Communicate your product requirements
- Communicate your packaging requirements
- Defining onsite tests and inline tests
- Defining your classification terminology
- Establish a perfect sample
- During production quality control process needs to be defined
- After production quality control process needs to be defined
By following the steps as laid out above you will be achieving products of the highest quality every time.
An insider’s tip!
Build a collaborative relationship with your supplier.
An often underrated element of preventing product defects is building a good collaborative relationship with your supplier. Go out of your way to develop this and it can have long term benefits for your organisation and the products that are manufactured.
IS COMPLIANCE A CHALLENGE FOR YOU?