How should importers of consumer electronics avoid a supply chain which includes suppliers who use child labour, have dirty and unsafe conditions, or who don’t follow labour rules? Here we endeavour to outline how a social compliance audit for consumer electronics can positively position your brand in the market place.
Conditions as mentioned above have made themselves all too familiar within the retail supply chain, and the worst part is that many retailers claim that they didn’t even know about this right up until before these tragedies became global news.
So how can we prevent this?
A social compliance audit.
This audit can go a long way in preventing some of the damaging issues many brands of consumer electronic products, and indeed other items, are all too familiar with.
A social compliance audit can be difficult to attain, but is an absolute necessity for that transparent supply chain your consumers today are demanding.
A social compliance audit ensures that a factory and its practices are abiding by all local laws and that you meet all of the social obligations as set out by the guidelines of the audit, from fair wages to no instances of child labor in a factory.
In this blog post, I will outline the exact procedure of this audit, the benefits it offers to your consumer electronics brand and how you can go about conducting this audit for yourself.
So, let’s dive in…
Document reviews – Auditors will check all the documentation of the supplier to determine the presence of any possible child labour, an all too common violation within the consumer electronics industry. They also assess whether there are any violations of extended working hours and wages. They will also look into what types of social insurance are available to workers and review any fire and safety documentation, which will help to determine whether or not any safety precautions or plans are in place. They will also inspect whether or not there is any environmental monitoring being done and, if so, how it is conducted.
Employee interviews – The auditors conduct interviews with the factory in question staff, where they ask them about their working hours, overtime, and about their holiday/leave time. Auditors also like to cross check these statements by interviewing factory management to ensure there are no discrepancies. This helps to clarify whether there are any instances of abuse or misconduct between staff and management. In the case of a re-audit these interviews will then be conducted again to ensure improvement plans are being implemented properly.
Closing meeting with audit status – This meeting reveals the audit results of your CE factory and also makes suggestion for improvements. If you use a qualified third party quality management provider to conduct this audit, they will provide you with an improvement plan and customize it according to your needs.
Continuous improvement – A reputable third party quality assurance solution provider will provide you with a plan of execution to rectify the shortcomings of a factory. To ensure the factory is executing the suggested improvements there are also unannounced visits by auditors to evaluate the factory’s improvement progress. Factories that attain a clean audit, will only be audited on an annual basis. In factories that achieve marginal results, they are often dropped in on unannounced and also receive audits on an annual basis. Factories that fail will then have a follow up audit again in a few months.
In understanding the ethical compliance standards as laid out above, you are able to make informed decisions about the suppliers you choose to use in the manufacturing of your electrical products.
Panasonic and Sony have been caught in supply chain scandals, that have created immense amounts of bad media coverage for the global electronic brands.
Accused of unfair labor practices in factories, with vastly underpaid staff and electrical components that are said to be sourced from parts of the world known to be inclusive of child slave labour.
With this in the media, consumers will begin to think twice about purchasing your product as they do not want to be affiliated with brands who are not achieving progress toward a transparent, sustainable retail supply chain as laid out by SA8000 guideline.
Can your consumer electronics brand afford publicity like this?
Achieving your social compliance audit will reduce any potential risks relating to the violations of global ethical standards, which puts your brand in a risky position and can cost your organization public shaming and embarrassment, scarring your brand. Dependent on the severity of the violation it could also cost you millions in lawsuits too.
This type of audit provides the desired transparency many consumers are looking for within the retail supply chain. Today’s consumers are becoming more concerned with the way in which products are sourced and manufactured, and rightly so.
So what are you doing to maintain consumer trust in your brand?

What can consumer electronic importers can expect from a social compliance audit?
Consumer electronic brands endeavour toward social compliance for these main reasons;- Brand protection
- To ensure your factory is clean and meets high levels of standards
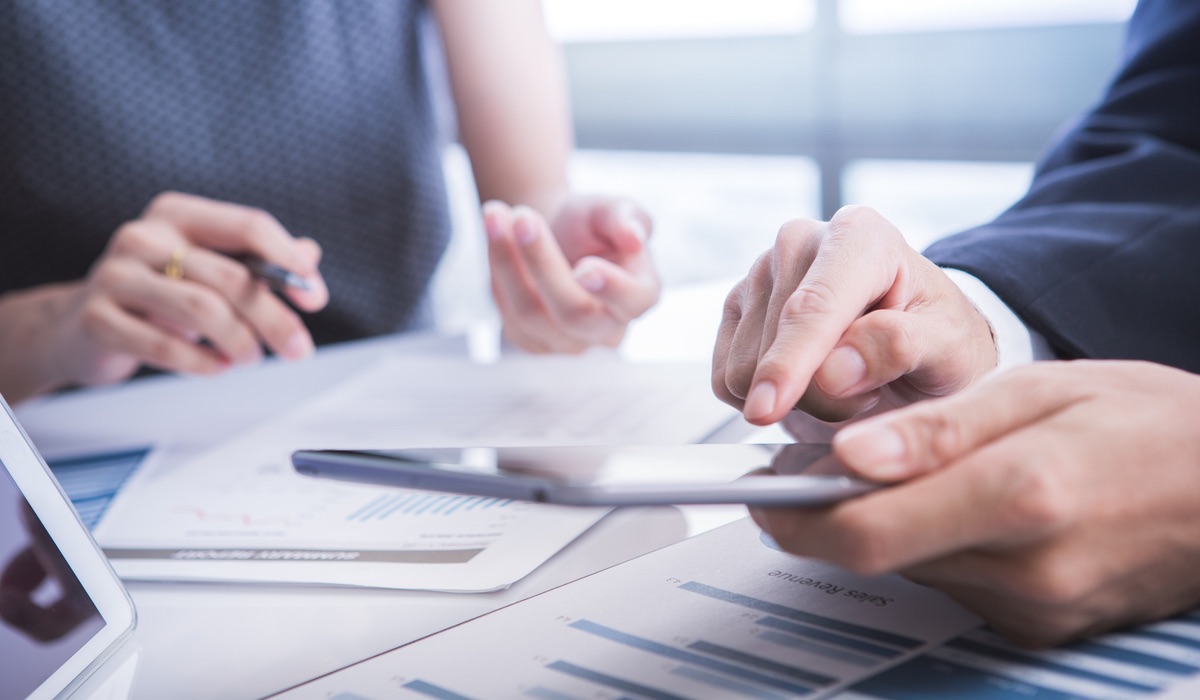
Protecting your electronics brand through a social compliance audit
Attaining a pass on your social compliance audit report is a commitment that your organization makes to ensuring that you are socially responsible and that you are committed to treating your factory’s staff ethically and in compliance with global ethical standards. So the question is… Is your consumer electronics brand committed to achieving an ethically responsible supply chain? Let’s take a look at the standards as laid out by SA8000: The 9 SA8000 social compliance requirements are:- Child labour – No children younger than 15 years of age may be employed by any factory.
- Forced labour – No person may be employed by a factory if they haven’t offered to do so voluntarily or be forced to work under the threat of punishment or retaliation.
- Health and safety – A safe and healthy workplace environment must be provided by the factory, who should also prevent any potential health and safety incidents and work related injury or illness from occurring. In the case of consumer electronics you would need to ensure that there is sufficient personal protective equipment within factories.
- Freedom of association and collective bargaining – All staff have the right to form, join and organize trade unions and to bargain collectively on their behalf.
- Discrimination – A factory is prohibited from engaging in discrimination in hiring, remuneration, access to training, promotion, termination or retirement.
- Disciplinary practices – A factory is prohibited from engaging in or tolerating the use of corporal punishment, mental or physical coercion or verbal abuse of employees.
- Working hours – A factory must comply with applicable laws, collective bargaining agreements and industry standards on working hours, breaks and public holidays.
- Remuneration – The right of staff to a living wage must be respected by the factory.
- Management systems – Compliance must be reviewed and implemented to the SA8000 standard through developed policies and procedures.

Who should conduct your factory’s social audit?
Many suppliers choose to conduct their own audits with in house teams, this method is untrustworthy which can produce bias results of the supplier.
Unless you have an extremely good relationship with the supplier in question and know for a fact that they are not going to lie on your audit report, then this way of passing a factory social audit is not our recommendation. Hiring an impartial third party quality management provider may be the answer They are viewed as independent parties with all the technical expertise to be able to produce unbiased reports and provide you with actionable improvement plans for you to progress forward in achieving your factory’s social compliance.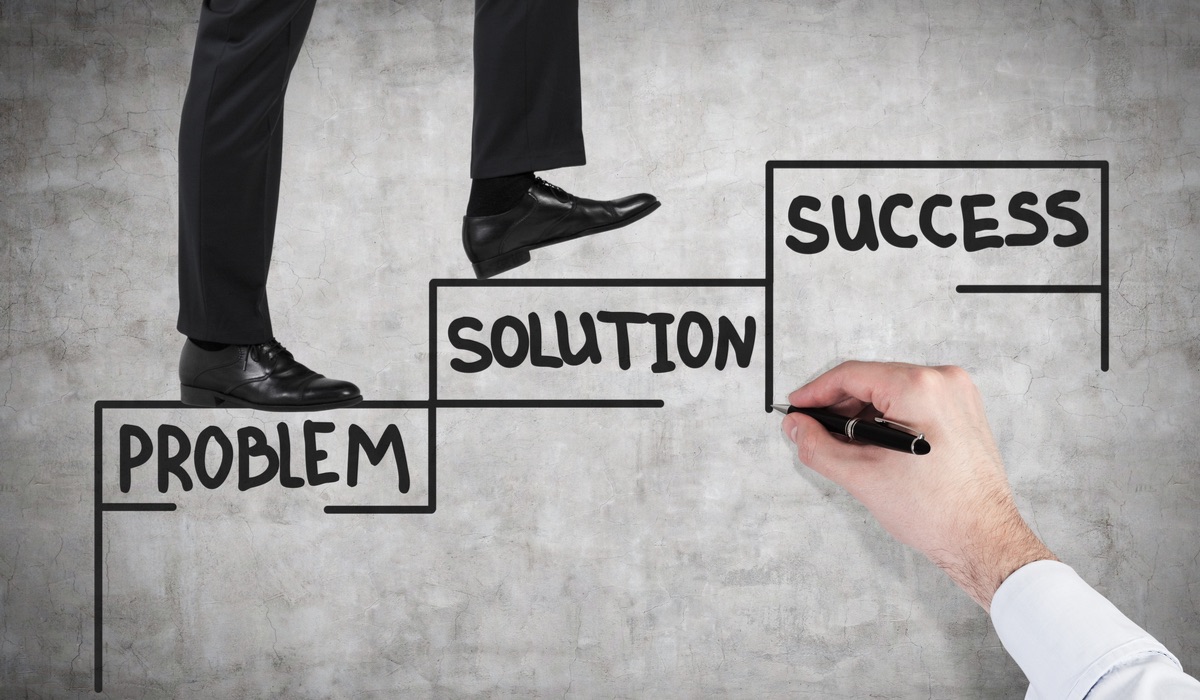
Independent audits are also taken into higher consideration by NGO’s and the media to be a truer and an honest reflection of the findings within the factory.
By outsourcing this service you not only are able to protect your brand’s image, but you minimize any potential risks you might face by not having a social audit, that can prove to be costly for your brand in many more ways than just revenue loss. Many consumer electronic factories are still found in violation of unfair labor practices or extensive work hours. This doesn’t have to be… Let’s take a look at what Apple has implemented when underage labor is found within their factories; “If we find underage workers in our suppliers’ factories, we make the suppliers return the children to their homes, pay for their education at a school of their family’s choice, and continue to provide income for basic needs until they reach the legal working age. We also enlist a third-party organization to monitor the children’s progress and report back to us. After they complete their education, suppliers must offer them reemployment. In 2015, we found three cases of underage labor — and we will continue to look for it.” Apple has shown that ethical and fair practice within your factory is not impossible to attain. It will be up to you to implement an appropriate strategy to deal with the social challenges felt within consumer electronic factories. Apple is a global leader for consumer electronics, but is also innovating in the way that they say no to injustices in a supply chain and go above and beyond to achieve an ethical and fair supply chain to produce the high quality electronics that they offer. Are you willing to do what it takes to achieve that transparent supply chain? API can help you attain this goal as your third party auditing partner. Have you undertaken SC audits across your CE supply chain? If you have any question about factory social audits, feel free to contact us and we will be pleased to answer them and help where we can.